Couplings
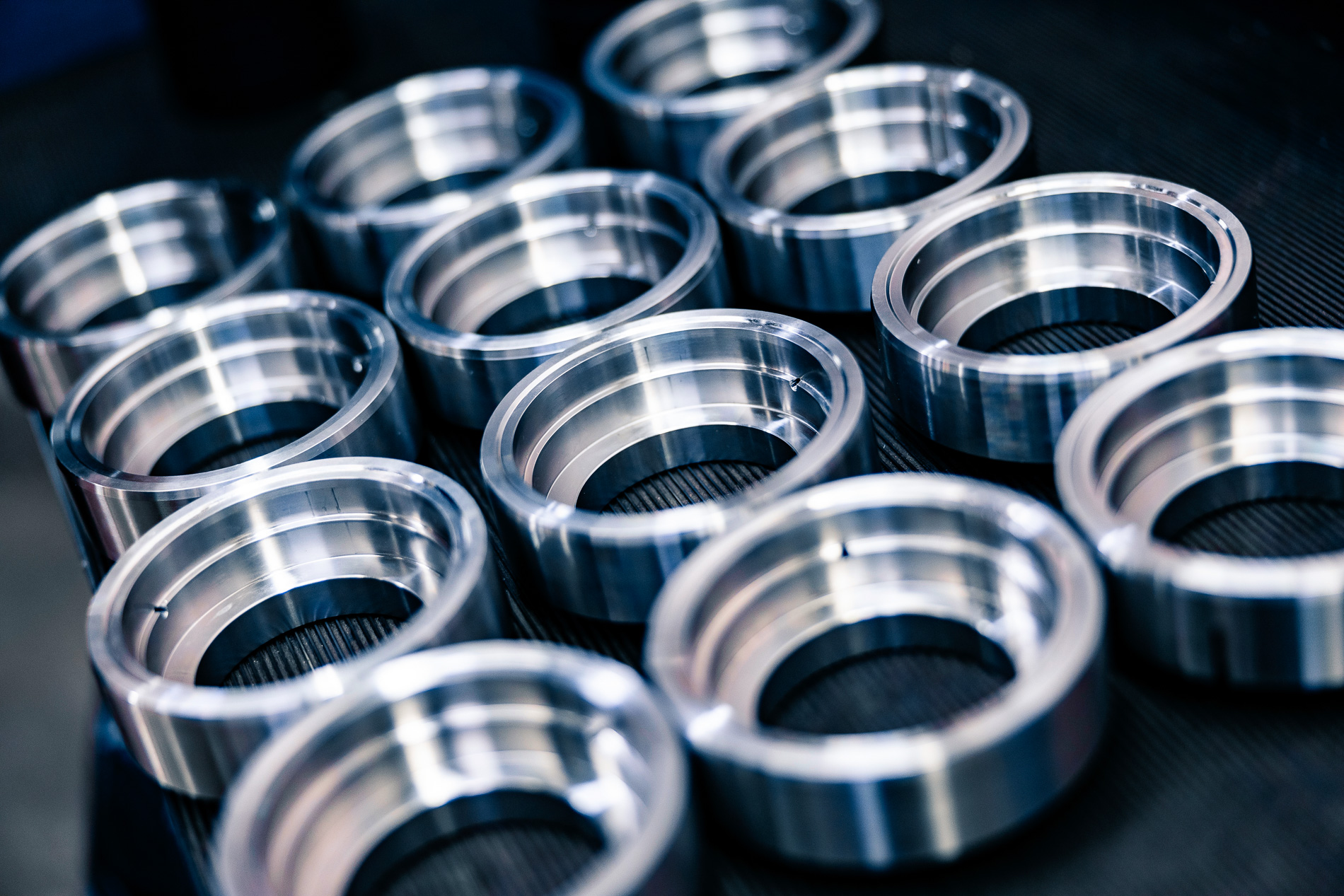
Our coupling solutions
We tailor our coupling solutions according to the individual needs of our customers. Power Tech Group’s own coupling family includes:
- Gear couplings
- Pin couplings
- Claw couplings
- Shear pin couplings
- Disc pack couplings
- Flange couplings
- Clamp couplings
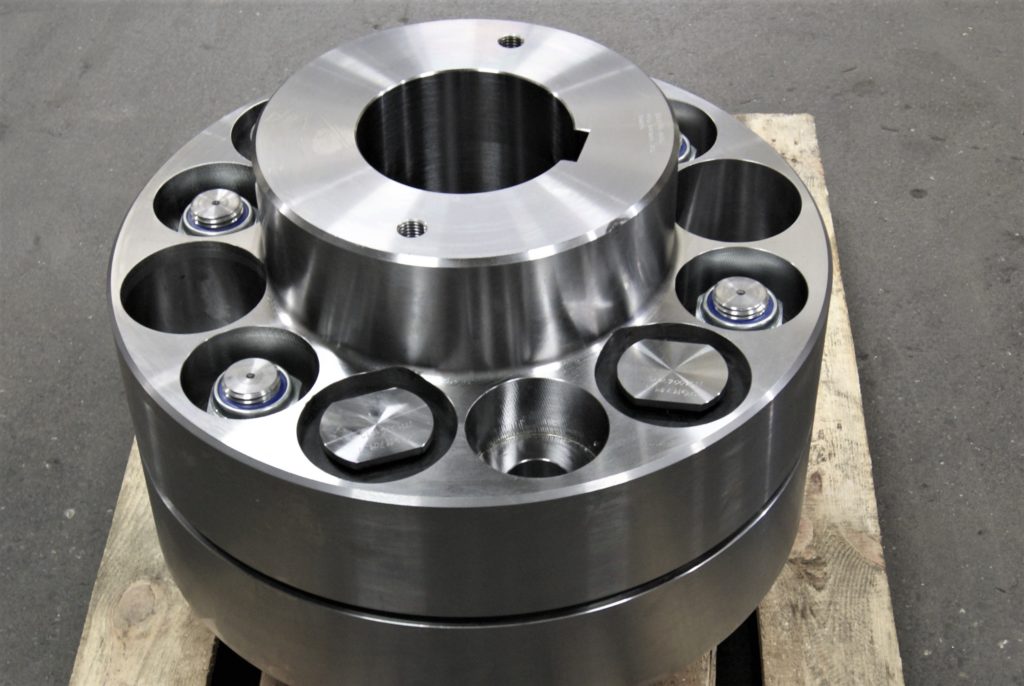
GC gear coupling ja CGC claw coupling
GC gear coupling is a torsionally rigid coupling, which can transmit a high torque when compared to its physical size. The crowned gearing can compensate for angular and radial misalignments between the shafts, and even long axial strokes can be achieved by altering the gearing length. The gear coupling is thus considered a flexible coupling. Torque is typically transmitted from the shaft to the coupling by a keyway and a fitted bore joint, and from the hub to the sleeve by the gearing. Torque is then transferred between the two coupling halves and thus from the driving machine to the driven unit by a flange joint. The gear coupling has a very long lifespan, when correctly dimensioned, and it is easy to tailor to fit almost any drive.
GC gear coupling line-up covers shaft sizes 150–1000 mm, and torques up to 16,000,000 Nm. Modern and flexible manufacturing methods make it possible for Power Tech Group to supply customized solutions with a quick delivery time. Special materials and heat treatments are available on request.
CGC Engagement claw coupling is one of the modifications of gear couplings. It is quite often used to connect auxiliary drive to be used in maintenance of the rotating machinery. For this speciality our product range is growing.
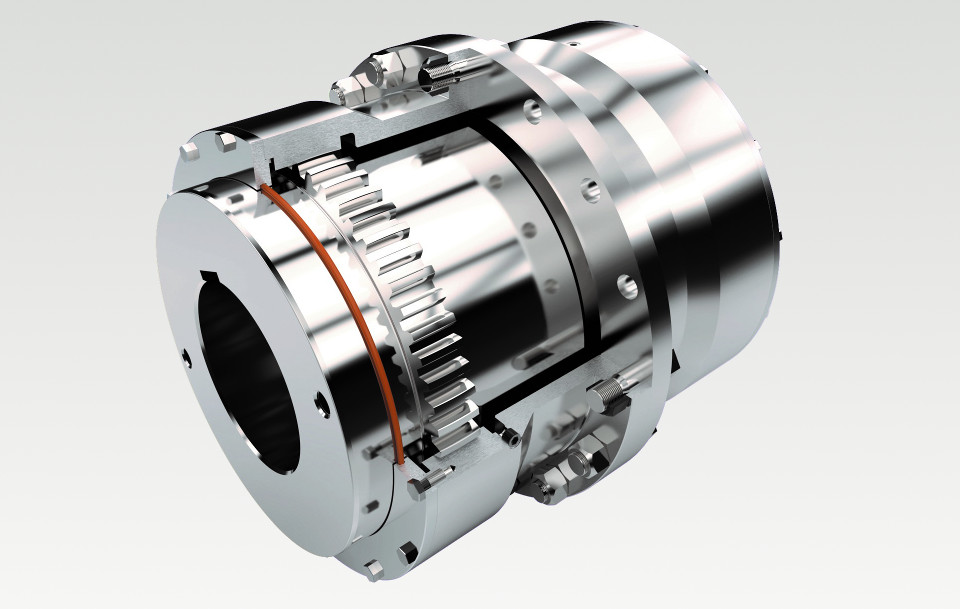
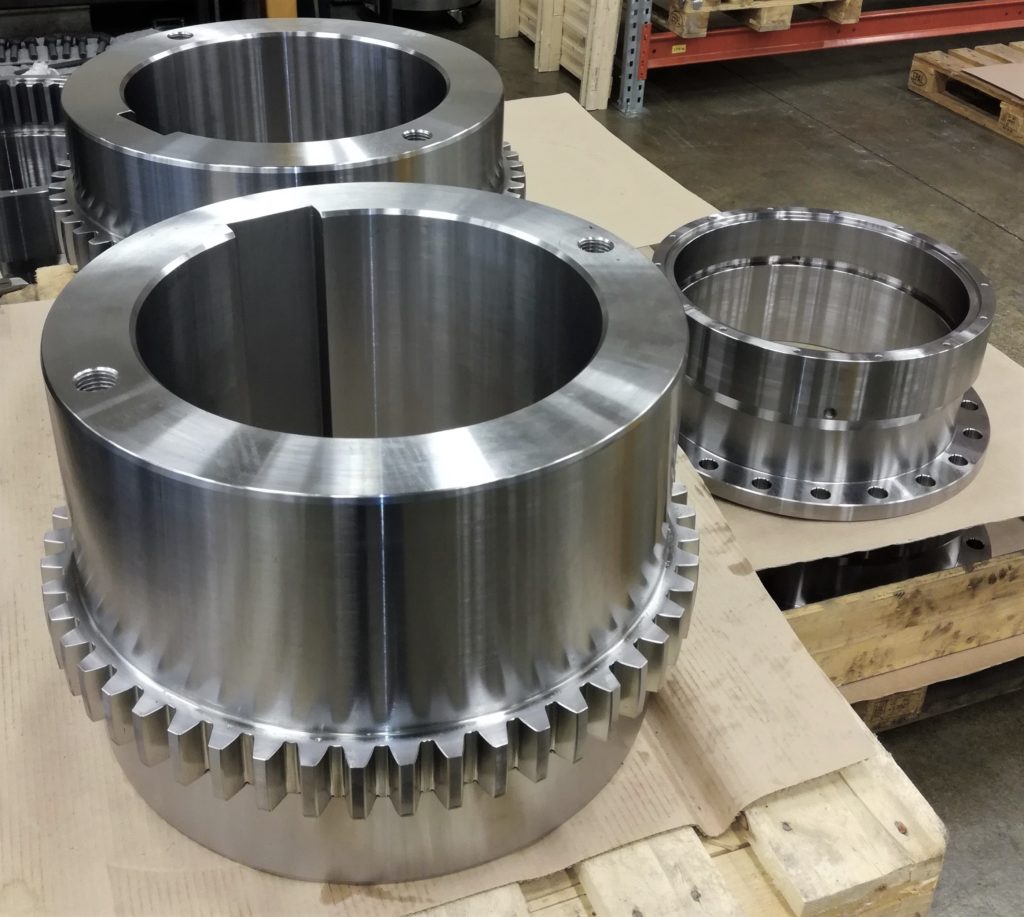
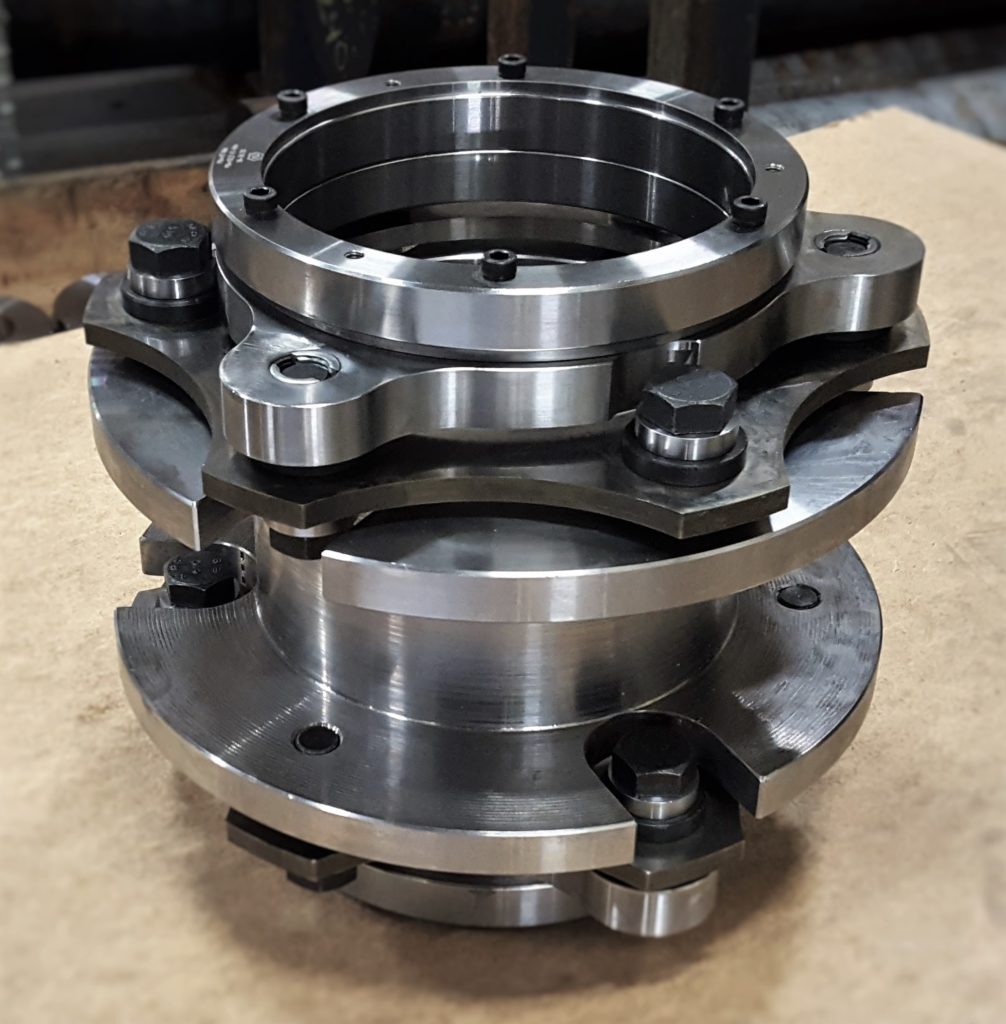
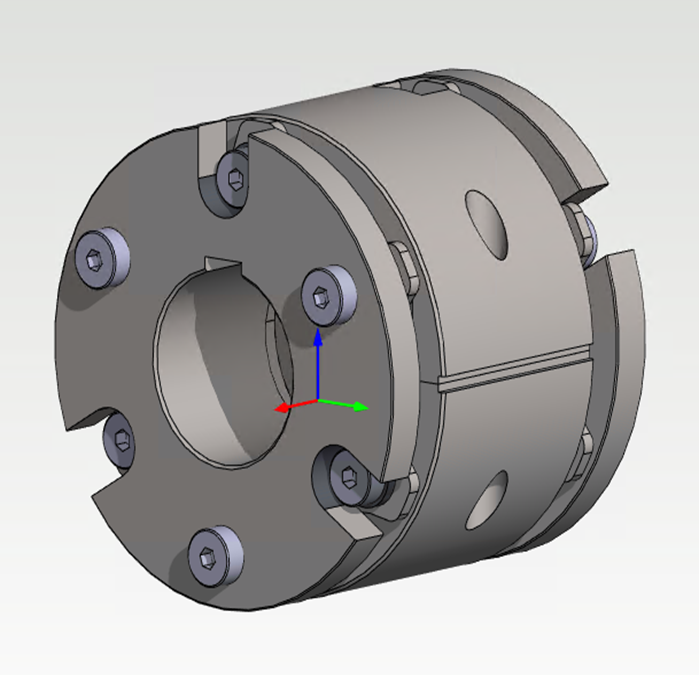
DPC and DPCC disc pack couplings
DPC metal discpack coupling is a torsionally rigid and backlash-free shaft coupling, which can compensate for medium angular and radial misalignments between the connected shafts. The all-metal construction is not susceptible to heat, and is maintenance-free, so the coupling is especially well suited for drives where traditional rubber element couplings cannot be used due to heat or high drive torque. A correctly installed and dimensioned discpack coupling lifetime is at least as long as that of the connected machines, and it requires no maintenance apart from visual inspection.
Power Tech Group’s DPC metal discpack coupling line-up covers shaft diameters 20–135 mm, but larger sizes are available on request. The DPCC version allows for a short distance between shaft ends (DBSE), and is equipped with a split spacer so that the machines do not need to be moved when changing the discpacks. The DPCC may also be used to replace a gear coupling, if maintenance-free operation is desired.
SPC shear pin coupling
SPC shear pin coupling is actually a part of a coupling. It can be integrated with another type of coupling, such as a gear coupling, or used alone to connect shafts. The purpose of the shear pin coupling is to quickly disengage the driving and driven machine from one another, in case of a sudden problem such as a short circuit. The shear pin can be customized to provide different shearing torques, which should always be somewhat higher than the highest maximum operating torque of the drive during start-up, for example.
The most common application for the SPC shear pin coupling are different test benches, where unexpected disturbances are common. Power Tech Group’s SPC coupling line-up covers shear torques of 5–140 kNm, but higher torques are available on request. The SPC unit consists of its own standardized parts and bearings, so that the same spare parts and pins can be used in different couplings.
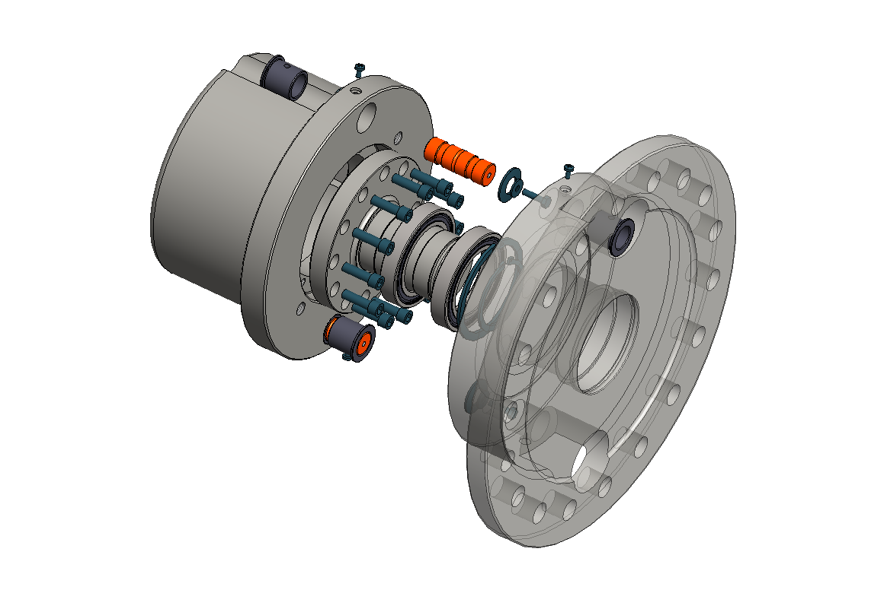
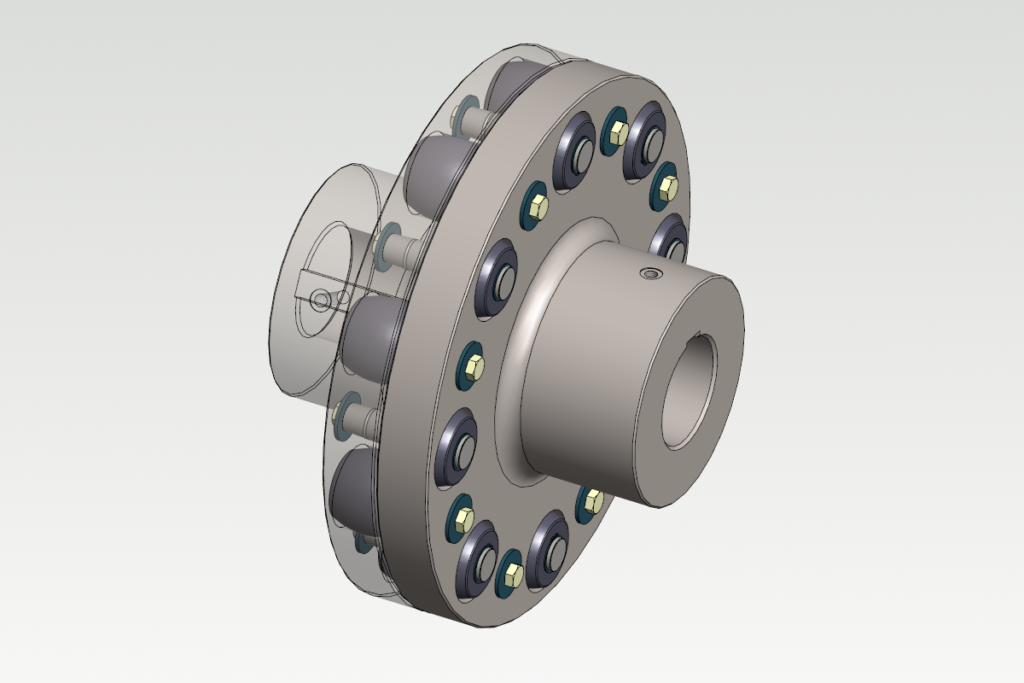
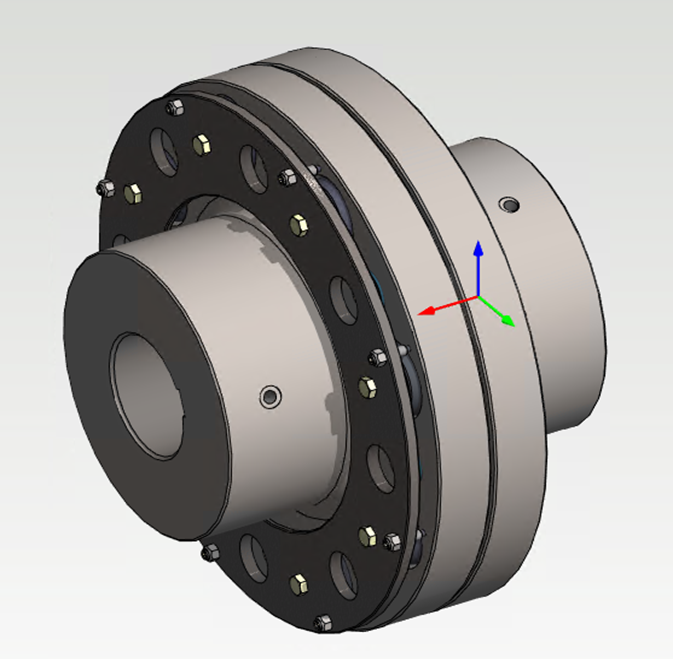
TK and TKR pin couplings
TK pin coupling is a tried and tested coupling, proven to be very reliable. The design allows for large angular, radial and axial misalignments between the connected shafts, and it also dampens vibrations. The pin coupling is especially popular in the mining industry, has a very long life time and requires no maintenance apart from visual inspection of the flexible elements. The flexible elements of the TK pin coupling can be changed without moving the connected machines, and are available in different materials for different operating conditions.
The TK pin coupling line-up covers couplings up to 1000 mm in diameter. For larger couplings (>1000 mm) please contact us. The TK pin coupling design can be easily customized to fit different drives, such as test benches. The coupling can also be combined with an SPC shear pin coupling, to provide a fail safe for the drive in case of sudden problems. The TKR coupling’s axial movement is limited so the coupling may be used with electric motors equipped with slide bearings.
Rigid couplings, clamp and flange types
KKT clamp coupling is a simple, rigid coupling for joining two machines together, or to be used as a shaft extension. The most common applications are overhead cranes and different drives in the saw mill industry, and also vertical mixers. The DIN standard clamp coupling is made of cast iron and is relatively large, whereas the PTG KKT clamp coupling is made of steel. This steel coupling is backlash free and much smaller than the DIN standard coupling, so it is especially well suited for drives with space limitations or high rotation speeds. The coupling can be installed and disassembled without moving the machinery, and is maintenance-free.
KKT clamp coupling line-up covers shaft sizes of 30–150 mm, but even larger models are available on request. Different materials, such as stainless steel, are also available. The FC Flange coupling is used more or less for the same purpose. Thanks to its ability to carry bending moment, the coupling is used in applications where the driving gearbox and electric motor are “hanging” on a driven shaft. Sizes up to 600 mm in shaft diameter are available.
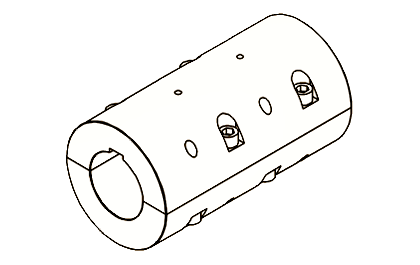
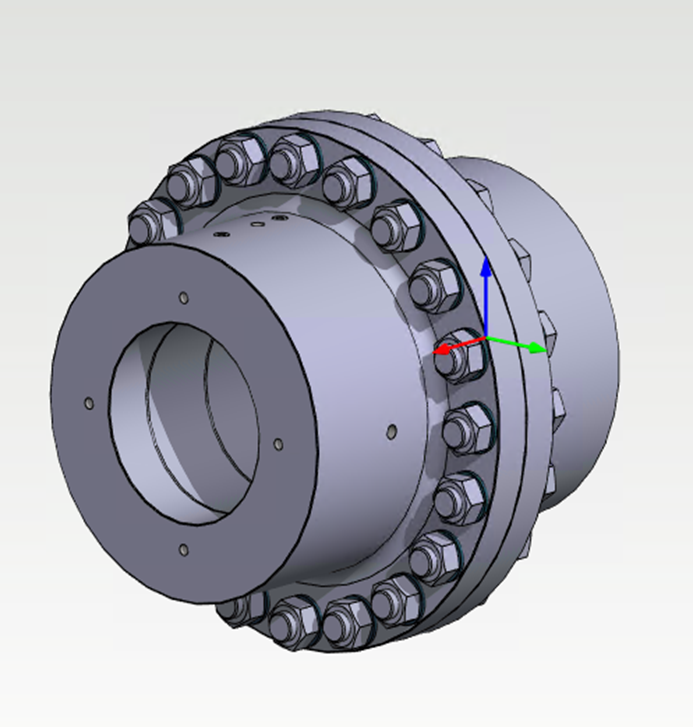